The Alfa Laval Filter (ALF) constitutes of a range of automatically selfcleaning filters/strainers, used mainly to protect heat exchangers from clogging, fouling and corrosion in various industries where cooling systems use low-quality water. ALF removes debris and marine life, reducing the risk of unplanned downtime and prolonging heat exchanger service intervals.
- Home /
- ALF
ALF
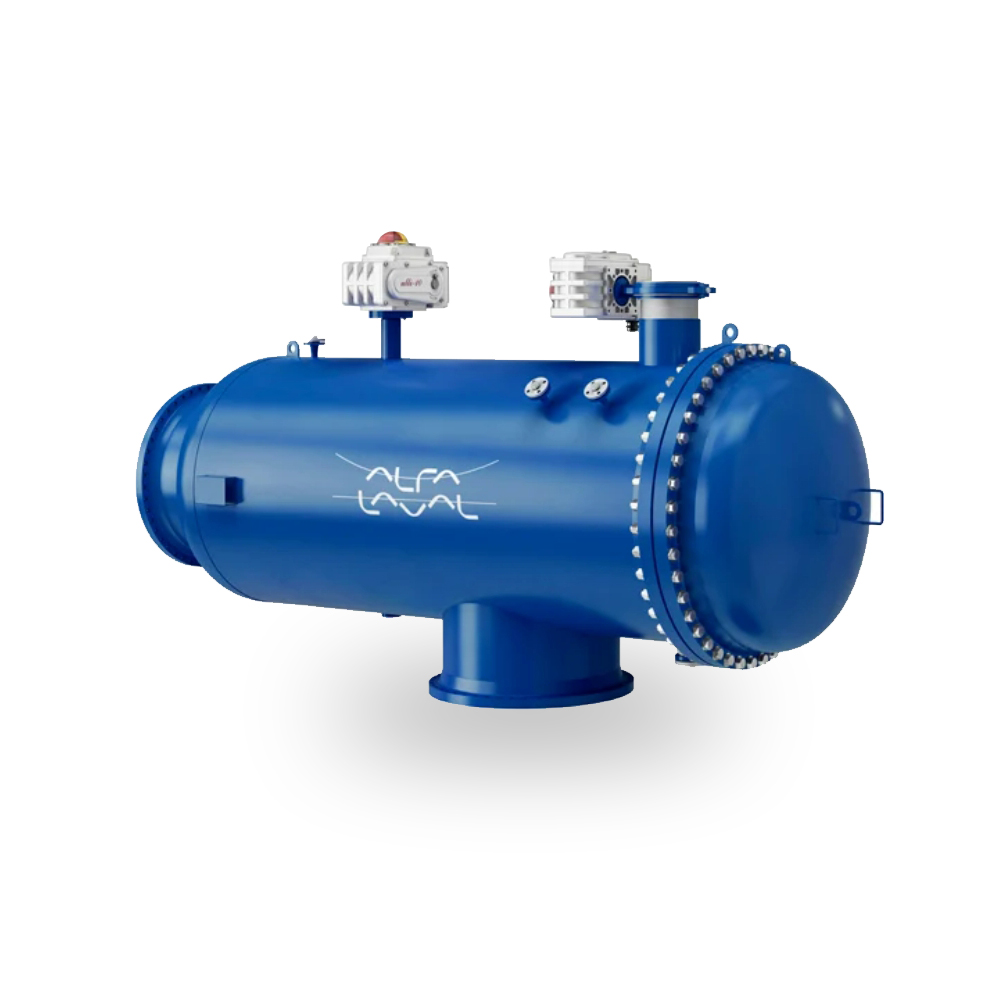
Documents
ALF is a pressure filter designed to maintain the thermal performance of plate heat exchangers and tubular condensers by making sure there is no debris or other undesirable materials in the water used in secondary cooling systems, via a highly effective automatic flushing set-up. Secondary cooling systems that use inexpensive, low-grade water have become widely accepted in industry, on ships and offshore installations, petrochemical plants and refineries, in power plants and in district heating and cooling systems. However, such water often contains undesirable particles, organisms and debris that can foul and clog the plate heat exchangers or tubular condensers used in such cooling set-ups.
Increase efficiency – protecting against clogging & fouling
Fouling, clogging and corrosion can have serious effects, reducing the efficiency of heat transfer and limiting the speed at which water can flow through the heat exchanger. This results in conditions in which biological growths can flourish, and surface fouling caused by diminished flow velocities.
The Alfa Laval Filter (ALF) is a supremely cost-effective way to avoid all these problems and ensure a reliable supply of clean cooling water. The system provides the major advantage of automatic flushing carried out at regular intervals, without interrupting the filtering process or disturbing cooling operations in any way. This provides crucial peace of mind for those responsible for process equipment downstream from the ALF installation.
Benefits
- Heat exchangers are protected from debris and marine life, which increases cooling system uptime and lowers maintenance costs
- Backflushing is performed automatically and does not interrupt the filtering process
- Easy installation and maintenance
- Proven, reliable technology
- Full support from Alfa Laval Service throughout the entire life cycle of the equipment
Reduce energy costs
The ALF also provides high filtering capacity with a low pressure drop, which cuts back on energy costs. By also minimizing the pressure drop across both plate heat exchanger and filter, an ALF installation helps reduce the overall costs of an effective cooling package. Because there are so few moving parts, maintenance costs are also low.
The ALF pressure filter has a casing made of stainless steel (ALF-S model), fibreglass-reinforced polyester (ALF-P) or rubber-lined carbon steel (ALF-R and ALF-B), and an internal cylindrical filter basket made of stainless steel. A range of different material specifications and mesh sizes are available.
ALF-B is a standardized model aimed at tasks where special options are not required. Just as the other models it offers reliable protection for your heat exchangers and fully automatic operation (backflushing).
The ALF design has the inlet directly in line with the filter and the outlet at a 90º angle. This ensures easy access to the filter basket without removing the connections, and makes it ideal for installation on any 90º pipe bend close to the equipment to be protected.
How it works
ALF can easily be cleaned either automatically at predetermined intervals, or manually by pushing a button on the control panel.
During normal operation, the liquid enters the filter basket, which is divided into an inlet section and a debris collection section by the flow diverter. The flow diverter is open and the flushing valve located at the outlet of the debris collection section is closed. The liquid passes through the inlet section where it is forced through the filter basket before then passing through the outlet. The velocity of the liquid is sufficient to dislodge and remove any matter embedded in the inlet section of the basket.
In primary flushing, the flushing valve opens the flushing outlet, thus increasing the total flow through the filter. This loosens any debris sticking to the pipe walls and to the filter basket. This debris is flushed out to the drain through the flushing valve.
In secondary flushing (commonly known as backflushing), the flow diverter closes while the flushing valve remains open. The liquid flow is then diverted and forced to pass through the filter basket in the inlet section. The majority of the liquid leaves the filter through the main outlet but the pressure in the filter draws part of the flow from the exterior to the interior of the debris collection section. This provides a backflushing effect on this section of the filter. Any dislodged material is discharged through the flushing valve.